Installation integrity
The relationship between a floor covering, an adhesive and a subfloor.
Craig Thornhill, Technical Services Manager
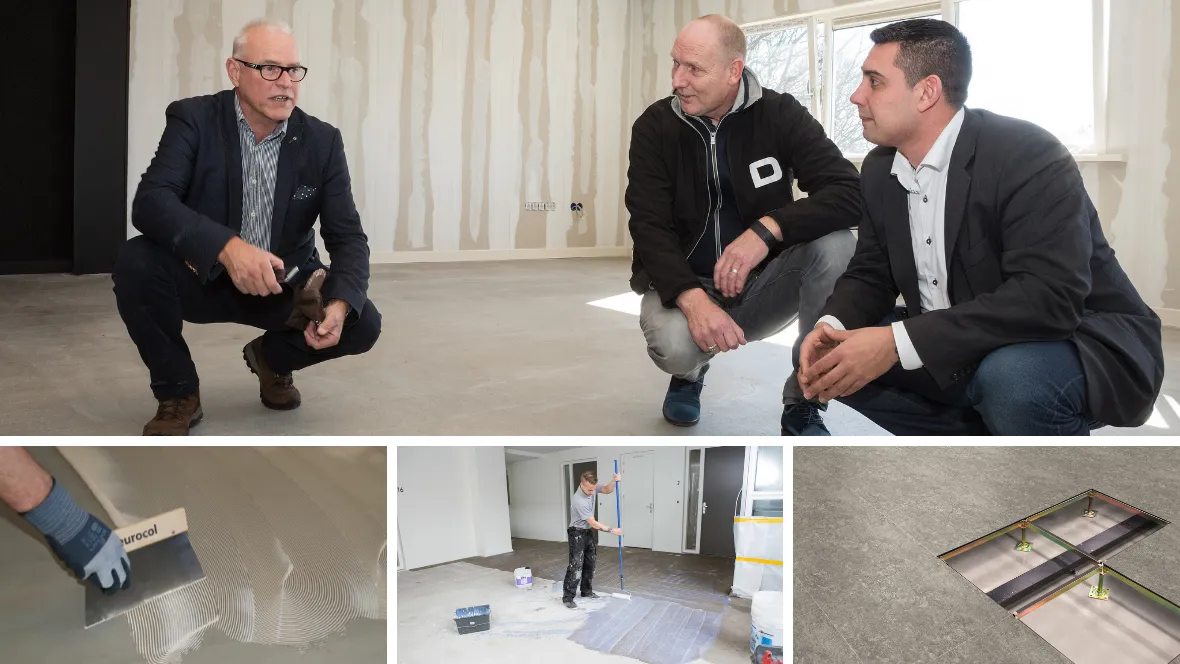
As a floor covering and adhesive manufacturer, Forbo is well positioned to understand the important relationship that exists between a floor covering, an adhesive and a subfloor.
The successful installation of a floor covering designed to be fully adhered is reliant on the selection of the correct adhesive, a suitable prepared subfloor and the recommended fitting guidance for all products being followed. Any breakdown in that sequence can lead to the installation integrity of whole or part of the fitment being compromised and potentially failing. This article is designed to highlight some of the ‘must do’ and ‘best practice’ actions to ensure successful installations time after time.
The obvious ‘must dos’ are compliance with the relevant British Standards (BS8203 for resilient flooring, BS5325 for textile floor coverings and BS8210 for wood and wood-based panels) and specific installation guidance provided by the manufacturers or suppliers. It is quite common for similar type products from different manufacturers to require varying fitment techniques or adhesives, such as in the case of luxury vinyl tiles. The British Standards have been compiled to provide practical guidance for subfloor preparation, site conditions before, during and post installation as well as detailing requirements for acclimatisation of products before fitting.
Whilst there is very specific guidance for resilient floor coverings in BS8203:2017 Section 7.4 all flooring materials, prior to installation, should be allowed to become acclimatized to the site conditions in the laying area.
Adequate acclimatisation and following manufacturer’s storage conditions will help to ensure that the adhesive is at its optimum workable consistency.
BS8203:2017 Section 7.4 states that:
Prior to installation, flooring materials should be allowed to become acclimatized to the site conditions in the laying area.
Adhesive technology has moved on a lot in recent years and with it, the way they work and behave. Being a long serving member of the flooring industry (heading for nearly 40 years now), my memory goes back to the days when there was less choice of both adhesive and floor coverings. You could say life was easier and less complex then, but, the same basic rules of engagement existed then as now – follow British Standards and manufacturer’s guidance. But, importantly, modern floorings and adhesives do not perform over damp bases, so testing for residual moisture is a ‘must do’ requisite before any fitment over solid substrates.
At this point, it would be remiss of me not to mention primers. There is a wide selection of primers available for all types of substrate and application. Primers can be very helpful for absorbent surfaces to promote adhesion and to prevent unacceptably rapid drying of adhesives (basically helps to prevent the adhesive being quickly absorbed into the substrate). Primers are very useful when applying a tackifier adhesive over porous substrates and I have many memories of attending sites to view a ‘less than tacky’ surface due to the adhesive ‘disappearing into the substrate.
So, many things have changed, and we now have more floor covering types (different backings, usage and fitting) which means even greater need for ‘due diligence’ when choosing adhesives. So be careful - an adhesive you used for one flooring may not be right for another - just because the only tub of adhesive in your van happens to be your ‘favourite adhesive’ does not exempt you from checking for official approval of suitability rather than assuming it will be alright. Five minutes spent checking is better to avoid experiencing problems later, like having to rip up and replace a floor.
I know from experience that some floor coverings are more sensitive to certain types of adhesive. One such result of sensitivity is plasticiser migration with vinyl flooring which can occur due to non-compatible adhesive application or leftover residues, creating a chemical reaction within vinyl flooring. Plasticiser is the component within vinyl that provides the flexibility and when plasticiser migration happens, sheet vinyl can soften, discolour, loosen, crack or turn brittle and results in a breakdown of the adhesive, basically causes the adhesive to emulsify and lose tack.
It is irreversible and, in most cases, requires the flooring to be uplifted and replaced. But it does not happen overnight. It can be several months after installation, even after the 12-month snagging period, before any indication of a problem. It is important to know about and understand the causes for this problem in order to avoid mistakes before or during fitting, so that the potential for risk is minimised.
Whilst adhesive selection is important, so too is adhesive application. For the various adhesive types available, there are different recommended ways to apply. It could be the traditional trowelled on application or by roller or both. What is key to a successful adhesive application is ensuring the correct method is adopted. An example is a tackifier adhesive which is designed to be rolled on as an all-over application, if applied with a trowel will provide only partial contact with the floor covering and potential problems with limited adhesion.
Mentioning trowels, it is important to use the correct trowel type (notch size) recommended for the different types of adhesive. An example is linoleum which needs a higher amount of adhesive applied (large notch size with a sharper point) to ensure the adhesive beds into the hessian backing and underside of the product.
BS8203:2017 Section 7.4 states that:
The depth of spacing of the notches should be maintained throughout the installation
Similarly, heavily profiled backed carpets and artificial grass require a good spread of adhesive to sufficiently ‘wet’ the back of the product to ensure a satisfactory transfer.
The wrong trowel selection may affect the long-term integrity of the adhesive bond as will using a trowel beyond its useful life. Like tyres on a car, the notches on a trowel will wear down – the result being less adhesive applied. And obviously a clean trowel is a must have, as adhesive residues on the trowel will lower the notch size and could also cause cross-contamination with a different adhesive type being applied.
BS8203:2017 Section 7.4 states that:
The depth of spacing of the notches should be maintained throughout the installation
Keeping on application, it is important to know the open time of adhesives (the time before it ‘goes off’) and work within that to avoid the adhesive drying past its ‘tack state’ and late placement occurring. Late placement is where the adhesive has exceeded the open time and ‘firm’ adhesive ridges form. Whilst these can be tacky to the touch, the correct application (in the case of a semi-wet application adhesive) cannot be achieved.
I have been called back on many jobs where the flooring is lifting, only to find uncompressed adhesive ridges with no or limited transfer to the underside of the floor covering. If a floor covering is designed to be fully bonded, there should be an equal transfer of adhesive to both the subfloor and the floor covering.
A typical quote from adhesive manufacturers will be:
Apply the adhesive evenly onto the substrate using a suitable notched trowel and leave a short open time according to quantity applied, climatic conditions and substrate absorbency. Only apply as much adhesive as can be covered within the working time.
Climatic conditions relate directly to temperature and humidity. The higher the temperature, the more moisture retention the air has, and so ‘wet’ adhesive will dry quicker. The reverse happens in colder conditions, on damp days it takes much longer for the adhesive to dry. Hot weather, particularly direct sunlight, must be considered when spreading adhesive to avoid too large an area being covered than the fitter can fit in the now shorter working time of the adhesive.
Raised access flooring (RAF) is used extensively in today’s office environments with the need for access to the underside for services such as heating pipes or cabling. There are resilient and textile tile and plank type product options on the market suitable for such areas which require securing to the RAF panels. The standard application method is to adhere using a tackifier type adhesive (an adhesive that stays ‘tacky’ for its working life) which allows tiles/planks to the lifted as required for access. The application of tackifier over RAF panels should be ‘all over’ not just in places, and with enough quantity of adhesive applied, to avoid the installed flooring lifting or doming.
Finally, provision must be made for a consistent temperature (between 18 and 27 degrees Celsius) for the first 24 hours of an adhesives bond formation to avoid movement at joints. BS8203:2017 states in Section 7.4 The laying area should be at a steady temperature between 18 °C and 27 °C for at least 48 h prior to, during and for at least 24 h after completion. The minimum subfloor temperature should be 10 °C.
Provision should also be made for ventilation throughout and after installation.
It is also important to allow the bond to develop fully before allowing the area to be trafficked, particularly by heavy wheeled or foot traffic.
In closing, my simple message is to check and double check all aspects of an installation. It is safer to take time to do that than just ‘take a chance’. Manufacturers and suppliers would prefer to spend time before a project starts in providing advice and guidance rather than having to go to a site to discuss what is, on many occasions, a problem due to an avoidable mistake.